Seven Workplace Fatalities
- Tracey Murphy
- Aug 8, 2017
- 2 min read
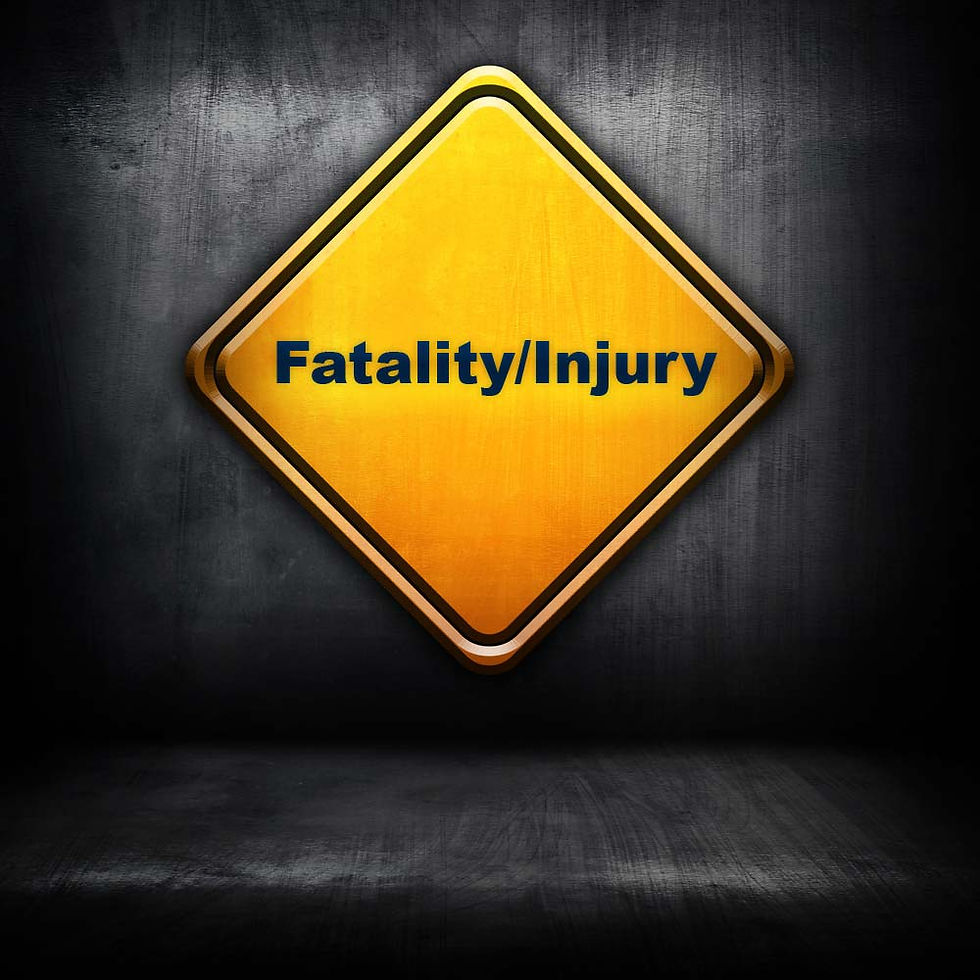
Recently WorkSafe NZ announced that there had been seven workers killed at work, in a three-week period. At least two were forklift related; one involved a swing lift.
It would be very easy to say that each of these people were in a place they shouldn’t have been, and that would probably be true. But, it is just the smallest part of the answer. It’s like saying wearing a hi viz vest will save your life. It will make you more visible, but it won’t make the injury less if you are hit or caught by machinery.
I have no inside information about these incidents, and am not making comment regarding any one of them. However, some basic rules apply:
Have a person in charge. Often this is the machinery operator but the important thing is that everyone knows who this person is.
Remove people who are not necessary for the activity.
Have a plan. Spend a few minutes discussing the activity. Identify the hazards and risks and put a plan in place to control them. Ensure that everyone knows and understands their role, including where they must be.
Agree on communication. Make sure that the hand signals, or whatever means of communication you are using, is clearly understood by all people.
STOP. If you can’t see someone who should be there, or who was in the area, stop operations until you know they are safe.
Job Safety Analysis (JSA) and Standard Operating Procedures (SOP)
A few years ago, a JSA was almost unheard of in smaller business; it was a tool used by large contractors. Smaller business used a hazard ID but, generally, nothing as complex as a JSA. This has changed and a JSA is expected in many situations. A JSA is a step by step analysis of the health and safety risks of an activity. It allows managers and workers to plan an activity safely. It can be completed by any person, with knowledge of the activity, but must be reviewed, discussed, and signed off by relevant workers before the activity begins. It must include site-specific hazards and risks. Used in conjunction with an SOP, there should be enough information to provide the workers with the safe, and efficient, method of carrying out the activity. JSAs and SOPs are similar in that they outline the activity step-by-step. However, a JSA is a hazard/risk assessment tool, while a SOP explains how an activity is done. Use these tools for hazardous activities.
My thoughts are with the families, friends and colleagues of each of these workers.
How can Safewise help?
We work with organisations who need more health and safety knowledge, or more time, than they have in house. We can assist setting up SOPs or JSAs working closely with those who execute the tasks.
Comments